鋁型材加工是將鋁錠通過一系列工藝加工成具有特定形狀、尺寸和性能的鋁制品的過程。
?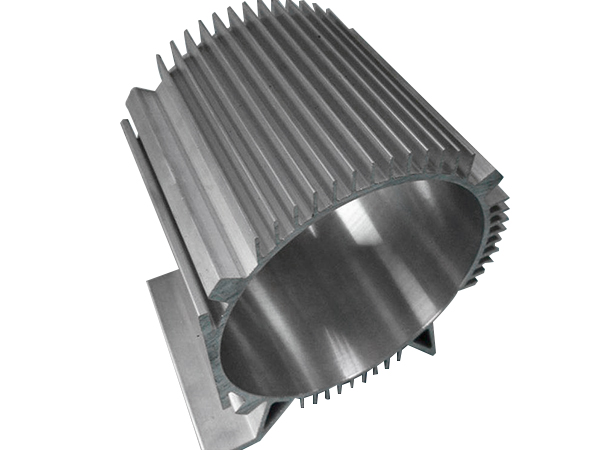
下面跟小編一起去看一看鋁型材加工過程中的質(zhì)量控制要點有哪些?
一、原材料檢驗
成分分析:采用光譜分析儀等設備對鋁錠及添加的合金元素進行成分檢測,確保其符合相應的國家標準或行業(yè)標準,如 6061 鋁合金,其主要合金元素鎂和硅的含量需在特定范圍內(nèi),以保證后續(xù)加工性能和產(chǎn)品質(zhì)量。
外觀檢查:查看鋁錠表面是否有裂紋、氣孔、夾雜物等缺陷,對于有明顯缺陷的原材料應及時剔除,避免影響加工質(zhì)量。
尺寸精度:檢查鋁錠的尺寸規(guī)格,如長度、寬度、厚度等,應符合采購合同或生產(chǎn)要求,否則可能導致后續(xù)加工過程中出現(xiàn)尺寸偏差。
二、熔煉與鑄造過程控制
溫度控制:精確控制熔煉溫度,溫度過高可能導致鋁液吸氣過多、合金元素燒損,影響鋁合金的性能;溫度過低則會使鋁液流動性差,導致鑄造缺陷。例如,對于一般的鋁合金,熔煉溫度需控制在 700 - 750℃。
精煉除氣:采用精煉劑等手段去除鋁液中的雜質(zhì)和氣體,確保鋁液的純凈度,可通過靜置、過濾等方式進一步提高鋁液質(zhì)量,減少鑄件中的氣孔、夾渣等缺陷。
鑄造工藝參數(shù):根據(jù)鋁型材的結(jié)構(gòu)和尺寸,合理調(diào)整鑄造工藝參數(shù),如冷卻速度、澆鑄速度等,冷卻速度過快可能產(chǎn)生鑄造應力,導致鑄件開裂;澆鑄速度過快易造成鋁液飛濺、卷入氣體等問題。
三、擠壓過程控制
模具質(zhì)量:模具的設計和制造精度直接影響鋁型材的尺寸精度和表面質(zhì)量,模具應具有良好的耐磨性、強度和剛性,定期檢查模具的磨損情況,及時進行修復或更換。
擠壓速度:控制合適的擠壓速度,速度過快可能導致鋁型材表面出現(xiàn)裂紋、拉傷等缺陷,速度過慢則會影響生產(chǎn)效率,一般來說,對于不同規(guī)格和材質(zhì)的鋁型材,擠壓速度在 0.5 - 5m/min 之間。
溫度均勻性:確保擠壓過程中鋁坯料和模具的溫度均勻,避免因局部溫度過高或過低導致型材變形、尺寸偏差等問題,可采用加熱裝置和溫度監(jiān)測設備對擠壓過程進行實時監(jiān)控。
四、表面處理質(zhì)量控制
前處理:在進行陽極氧化、電泳涂裝或粉末噴涂等表面處理之前,需對鋁型材進行除油、除銹、堿洗等前處理工藝,以確保型材表面清潔、無油污和雜質(zhì),提高涂層與基體的結(jié)合力。
工藝參數(shù)控制:嚴格控制表面處理的工藝參數(shù),如陽極氧化的電解液濃度、溫度、電壓和時間等,電泳涂裝的漆液參數(shù)、電泳電壓和時間,粉末噴涂的粉末質(zhì)量、噴涂壓力和固化溫度等這些參數(shù)直接影響涂層的厚度、硬度、耐腐蝕性和外觀質(zhì)量。
外觀檢查:表面處理后的鋁型材應進行外觀檢查,要求涂層均勻、無流掛、無氣泡、無漏涂等缺陷,顏色應符合設計要求,色差在允許范圍內(nèi)。
五、深加工質(zhì)量控制
切割精度:切割后的鋁型材長度偏差應控制在允許范圍內(nèi),一般要求長度公差為 ±0.5mm - ±1mm,同時,切割面應平整,無明顯毛刺和鋸痕,以免影響后續(xù)加工和裝配。
鉆孔精度:孔的位置、直徑和深度應符合設計要求,位置偏差不超過 ±0.5mm,孔徑公差控制在 ±0.1mm - ±0.2mm 之間,鉆孔時要防止出現(xiàn)偏斜、毛刺等問題,確??椎馁|(zhì)量。
折彎質(zhì)量:折彎角度應準確,偏差控制在 ±1° - ±2° 以內(nèi),折彎半徑符合設計要求,避免出現(xiàn)過度彎曲、回彈過大或表面開裂等現(xiàn)象。
組裝質(zhì)量:組裝后的產(chǎn)品應結(jié)構(gòu)牢固,各部件之間的連接緊密,無松動現(xiàn)象,產(chǎn)品的整體尺寸和形狀應符合設計圖紙要求,對角線偏差、平面度等指標應控制在規(guī)定的公差范圍內(nèi)。